Production & the environment
The activities of the Leyland Product Development Group have a major influence over the Environmental performance of the product range and include a large number of Environmental considerations.
These include the use of Selective Catalytic Reduction, Exhaust Gas Recirculation and Diesel Particulate Filtration technologies which are employed together to meet the latest Euro VI emission standard, which was implemented on all new EU market vehicles from 31st December 2013. This has delivered a 95% reduction in NOx and a 97% particulate matter reduction when compared to the Euro I standard introduced in 1993.
The greatest contribution to carbon reduction is through ensuring best fuel efficiency and the whole product range is recognised as being amongst the most economic on the road today, as shown in trade press road tests throughout the product range. There are a number of contributing factors to this performance including the use of lighter materials to reduce the weight and fuel use of the vehicles. Automated manual gearboxes are also offered where electronic gear selection reduces driver stress, improves fuel use and extends the service life of the transmission.
In addition at Euro VI other fuel saving features have been introduced including Vehicle Acceleration Rate Management and Driver Performance Assist, the latter of which provides the driver with positive feedback on his driving style to encourage fuel efficient driving.
We continue to develop and test new technologies which can contribute to both the environment and the future cost of operation of our vehicles.
-
Waste and recycling policy
Leyland Trucks has been actively involved in recycling and reuse of the waste produced at the site since 1996 and are constantly identifying and implementing improved techniques and processes with the aim of reducing our impact on the environment.
Between 1998 and the beginning of 2007 steady progress was made in reducing the amount of waste that we send to landfill from 75% (some 1000 tonnes per year) to 28%. And in 2007 we set ourselves the goal of reducing this to zero.
The ‘three R’s’
Our waste policy is based on the commonly used concepts of Reduce, Re-use and Recycle.
In cooperation with our suppliers we look to reduce packaging waste by designing reusable pallets for the supply of parts which both protect the parts from damage and can be used again and again. We also re-use some smaller items rather than throw them away. For example many types of plastic end-caps, which are used to protect the ends of pipes in transit, are segregated at the point of use and sent back to suppliers for re-use. Waste that we cannot We now recycle not only scrap metal, paper, cardboard and untreated wood but also, as a result of this project;
• Treated wood (which is used in bio-fuel plants).
• Polystyrene which can be used both in re-processed domestic polystyrene products and in road and bridge construction).
• Many types of plastic (which are re-processed and used in a variety of different products).
• Paint residue (which is burnt and mixed with other products to produce cement for use in the building industry).
• Our remaining “general waste” (now only about 11% of our total waste) which is sent to a local “Energy from Waste” plant where it is converted into electricity which is fed into the national grid. -
Energy Efficiency
Through detailed measurement of each utility (electricity, gas, compressed air and water) on a weekly basis, the Energy Management Team gains a detailed picture of Leyland Trucks’ energy needs. From this, the team is able to identify a plan of technical improvements that can then be applied to reduce the site’s energy usage. Specific examples of energy saving measures already implemented by the team include:
Energy saving light bulbs used throughout the plant.
Intelligent lighting used in the production facilities that control the amount of lighting needed at different times of the working day and ensuring lighting is not left on at inappropriate times.
All washroom facilities on site use automatic taps and reduced flush toilets to control the amount of water used by these processes.
All loading bay doors are fully automated to reduce heat loss from the plant.
Energy efficiency is an important factor in the selection of new equipment for use within the company.
HVAC control system upgraded to operate systems and control zones only when needed.
Leyland Trucks is also actively investigating the opportunities for sourcing alternative energies such as wind and solar power, biomass and energy from waste. -
Water Quality
Leyland Trucks has systems in place to reduce the amount of water used in its production processes and also to carefully control the quality of its wastewater discharge. Rain water drains and foul sewer drains are separate and are meticulously monitored and controlled to ensure that no harmful substances are incorrectly released.
All washroom facilities on site use automatic taps and reduced flush toilets to control the amount of water used by these processes.
The robotic chassis spray facility installed in 2005 uses a water-based abatement system to collect the paint overspray which is then removed and treated before the water is reused; this process allows the water to be used several times before it is treated a final time and safely removed from site in compliance with the appropriate legislation.
-
Air Quality/Factory Emissions
Leyland Trucks has implemented various measures in its state of the art production facilities to reduce its emission levels. These include:
• Eliminating toxic chemicals from our production processes wherever possible such as in the chassis painting process.
• The introduction of a robotic chassis paint plant in 2005, which has dramatically reduced the amount of paint overspray and emissions from this process.
• Promoting car sharing initiatives and providing showers and bike storage facilities to reduce traffic emissions from employees commuting to and from work.
The use of external consultants to help us identify further areas for improvement.
Related information
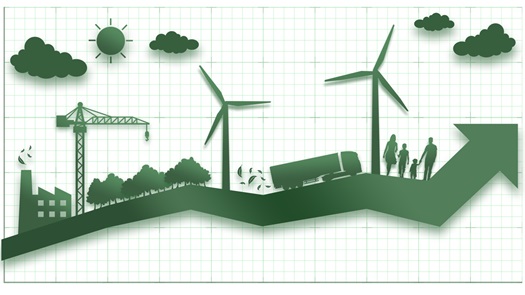
Environment
Leyland Trucks has had an environmental policy statement since 1995. This policy has led to the company recognising the actual and potential environmental impacts of its operations.
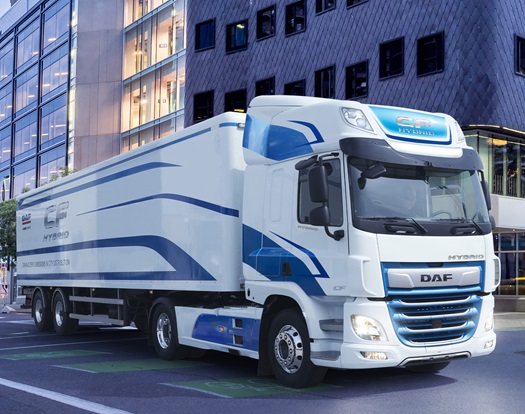
Our products
Significant progress has been made with regard to the impact of our trucks on the environment. Our current trucks are over 20% more efficient than the trucks we were making 20 years ago and emit 20% less CO2.
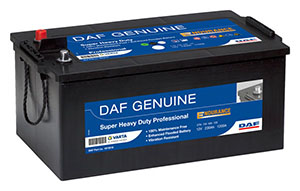
Automotive batteries
Leyland Trucks is obliged to collect waste automotive batteries for treatment and recycling from final holders.